Radiator TUBULAR FIN Machine
|
The Tooling and Developments Fin Machine will produce a flat copper fin for assembly of the Tubular Type Radiator Core, actual fin surfaces are designed specifically to customers requirements. The Machine is designed to enable the operator to quickly change the width of fin to be produced, fin length is controlled electronically and can be changed from one size to another in a matter of seconds. Incorporated with the Machine (illustrated) is the Automatic Fin Stacker, fins are cut to length and conveyed to the stacker, which stacks the fins in exact order to the core assembly operation. The Machine is available with or without the Fin Stacker dependent on customer preference.
| 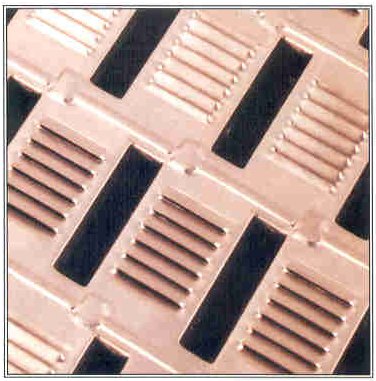 |
|
|
|
Radiator AIRWAY FIN Machine |
The Airway Fin Machine has been designed specifically to produce a quality radiator fin surface, of multilouvre design whilst maintaining a high rate of production, Fin length is controlled electronically, and change-over of fin width is particularly easy, to appeal to both the high volume producer and small manufacturer alike. The Machine is based on a modular construction comprising - coil holder, strip tension, rolling head, gathering and pitching units, quillotine (operated pneumatically), conveyer, etc. Maintenance and operation of this machine is particularly easy and does not require highly skilled operatives. |
| 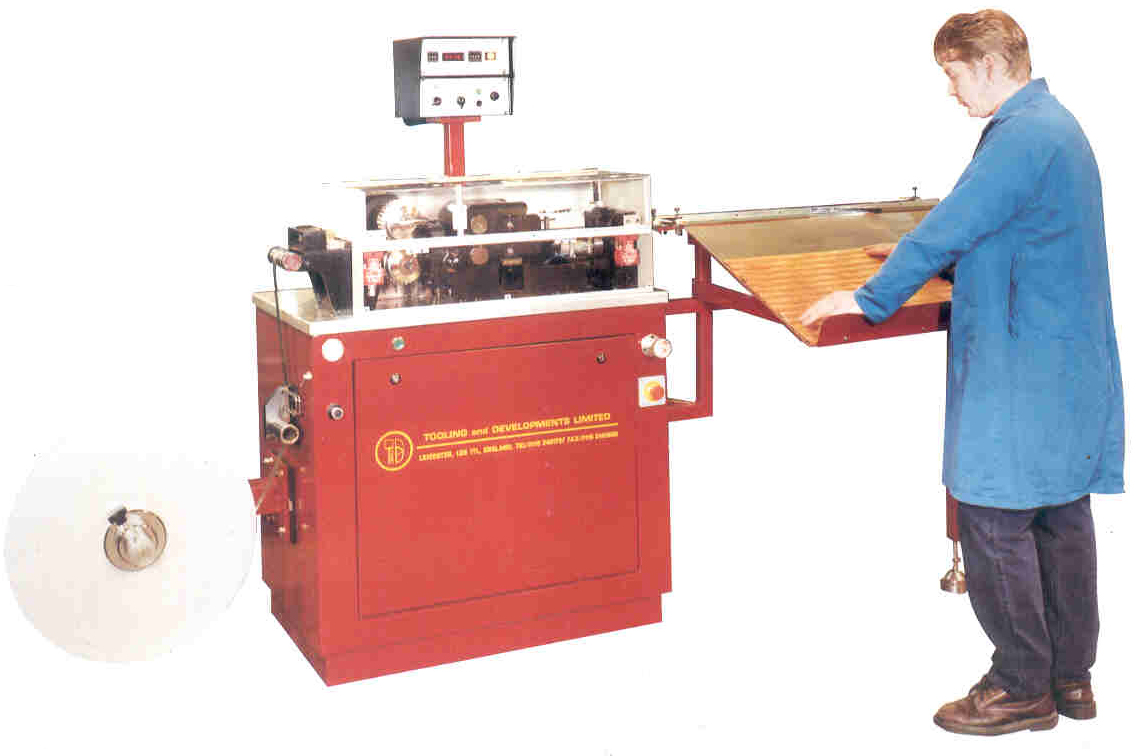 |
|
|
Radiator CORE ASSEMBLY Machine |
The radiator Core Assembly Fixture (McCord) is a versatile machine designed for rapid assembly of tubes, fins and header plates into a complete radiator core ready for the banking process. The design of the fixture enables various sizes of Radiators to be assembled using the same machine. The assembly platform is built around a sturdy aluminium base casting, onto which th pneumatically operated side and top clamps are mounted. Change over from one radiator size to another is both a quick and simple operation, requiring no special skills. | 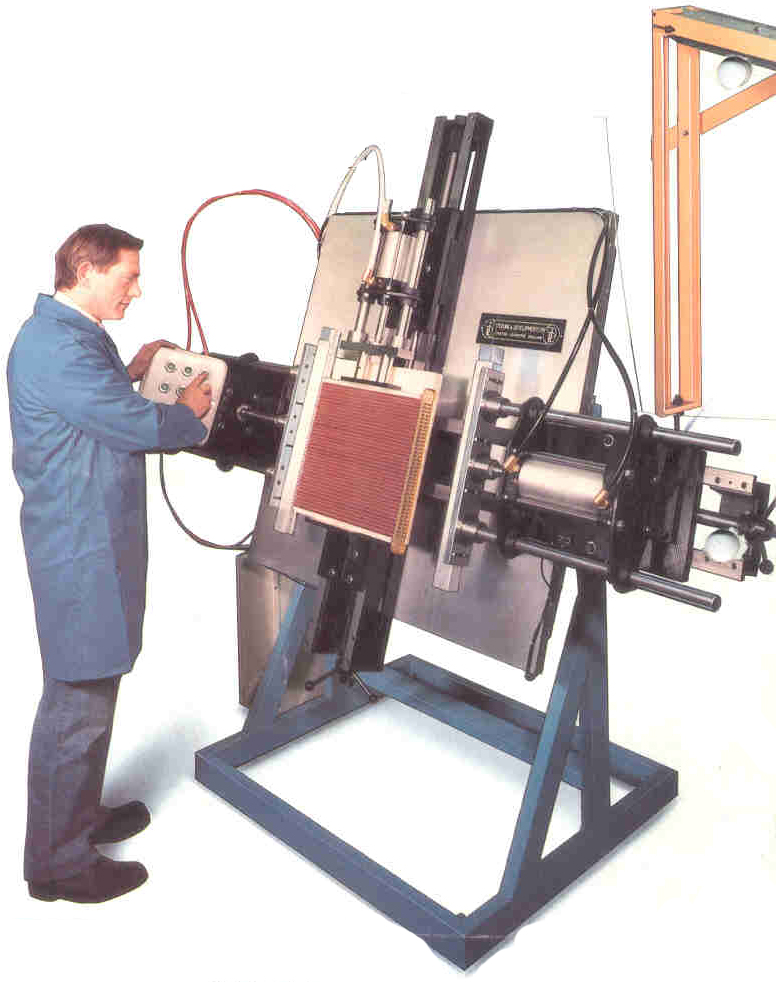 | 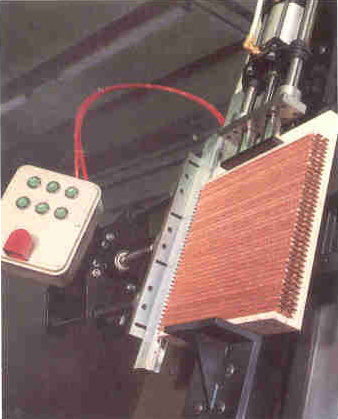 |
|
|
Radiator CORE TEST Machine |
The Radiator Core Test Machine provides a fast and efficient method of testing the finished product, whilst ensuring that under compression damage does not occur to the header plates. The inspection of the core is carried out by pressuring water, the fixture is easily adjusted for various sizes and is completely pneumatic its operation. | 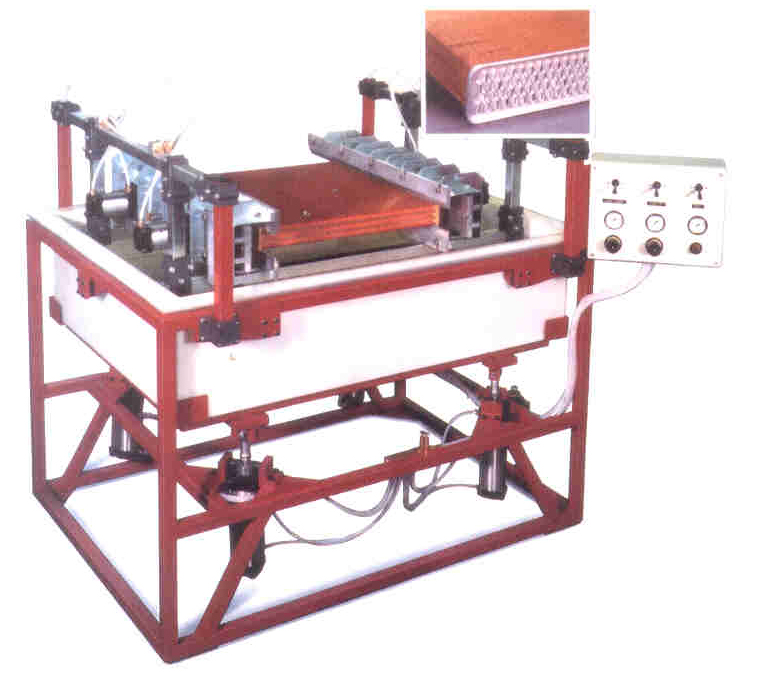 |
|
|
Radiator WATER TANK SOLDERING Machine |
The Water Tank Soldering machine, affords a fast and reliable method of soldering the Brass Tank to the Radiator Core. Compared to hand soldering, it is up to five times more efficient and for the operator a much cleaner process. The Machine is capable of accepting various sizes up to 750mm (30") in length.
| 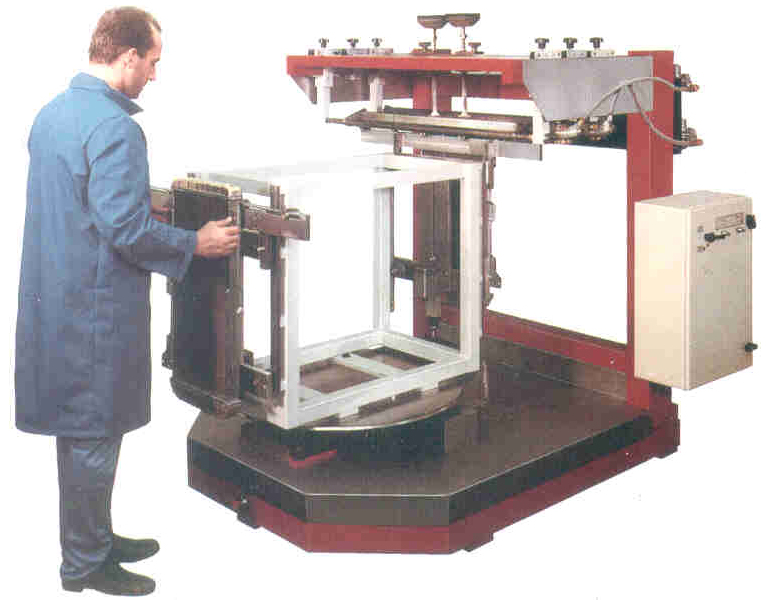 |
|
|
Header Plate SOLDER DIP Bath |
The Header Plate Solder Dip Bath is of heavy duty fabricated construction, electrically heated and insulated to give minimum heat loss, it comes complete with stand. Electric's are 380 / 440 volts 50 cycles unless otherwise specified by the customer. Temperature of solder is thermostatically controlled. The Bath is available in two sizes 120x30 cms (48"x12") and 60x30 cms (24"x12"), but can be made to individual requirements. | | The Header Plate Solder Dip Bath featured here, is essential for Plastic Radiator Cores where it is necessary to control solder deposits in order to avoid contamination of the rubber gasket recess. The Bath is electrically heated and is fitted width a variable speed pump, and is designed to accept most sizes of Radiator Core. The advantage for both Brass ad Plastic Tank Radiators being a noticeable reduction in Solder usage. | 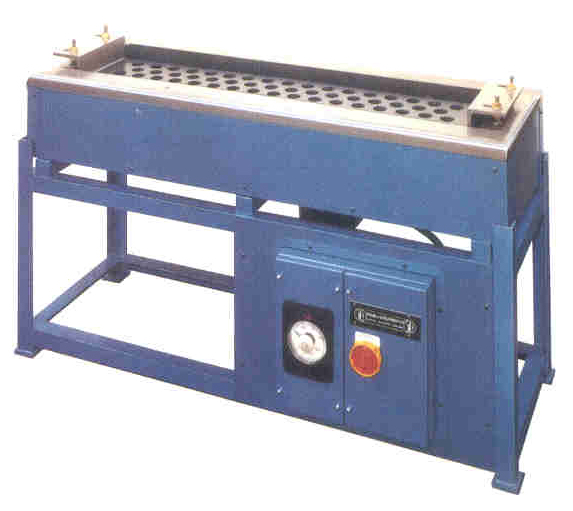 | | 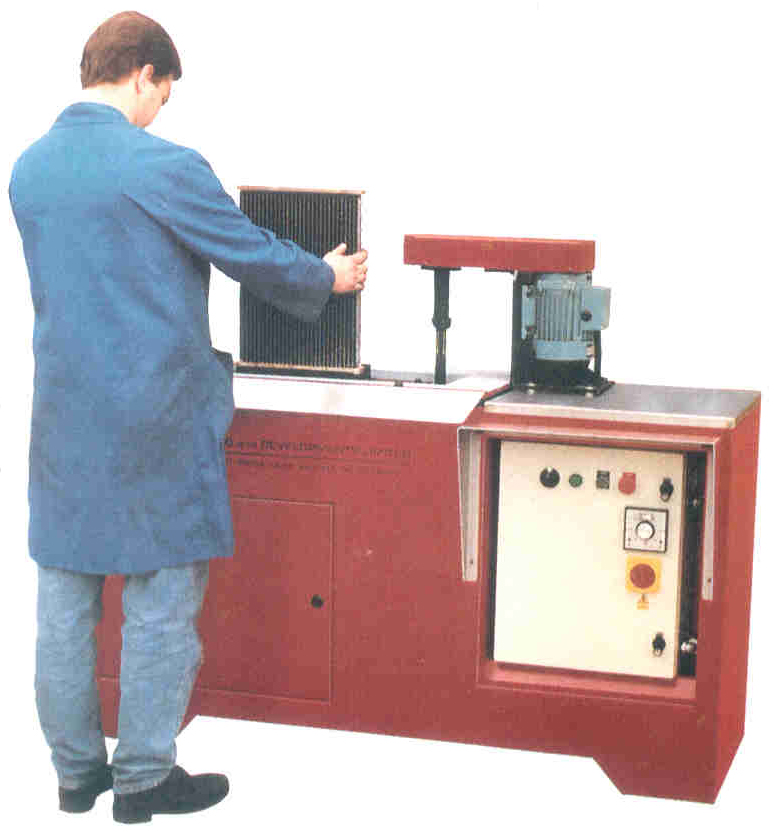 |
|
|
PLASTIC INJECTION & PRESS TOOLING |
Illustrated below are typical examples of our Tooling capabilities, we design and manufacture Plastic Injection Tooling for the production of Radiator Tanks, becoming ever more familiar with the move away from brass tanks. The Press Tool is a typical example of a header plate piercing tool, supplied o a quality die set with hardened pins and bushes. The working components are manufactured in high quality tool steel, hardened and ground. |  | |  |
|
|
Radiator TUBE FORMING Machine |
The Tube Forming Machine has been specifically designed to produce a Lockseam Radiator Tube externally solder coated and cut to the desired length. The tube itself is formed from a continuous length of untinned brass strip fed into the machine via a series of shaped rollers. From here the pre-formed tube passes through a cleansing and soldering bath where te external surfaces are soldered together to produce a watertight tube of superior strength. | |
|
|
Radiator TUBULAR ASSEMBLY Machine |
The Fin Assembly Table is a quick ad easy method of assembling fin and tube into a complete radiator core. It comprises an aluminium surface top ad bottom, accurately machined to a close flatness tolerance. Providing a rigid but light surface on which the extrusion can be mounted. The table can be opened or closed to accept various widths of radiator core by means of a chain linked winding down mechanism to all four corners, and is manufactured in a number of sizes from 60x60 cms (24"x24") up to 150 cms (60"x60"). | |  |
|
|
Radiator CORE BAKE Oven |
The radiator Core Bake Oven is constructed from high grade Stainless Steel to withstand corrosion, and heated electrically by six porcelain elements totally enclosed in a stainless steel sheath, giving a capacity of 24 kW. Access to these elements is arranged by a fan, situated in the roof of the oven, forcing the air through the Radiator Core. The Work Chamber will accommodate 1270mm x 1270mm x 300mm (50"x50"x12"), fitted with pneumatically open and close door for ease of loading. Temperature is automatically controlled, with a separate timer for length of baking time required. This are all situated on the main oven control panel. The oven is supplied on its own rigid stand and electric's are 380 / 440 volts, 3 phase 50Hz, unless otherwise stated. | | 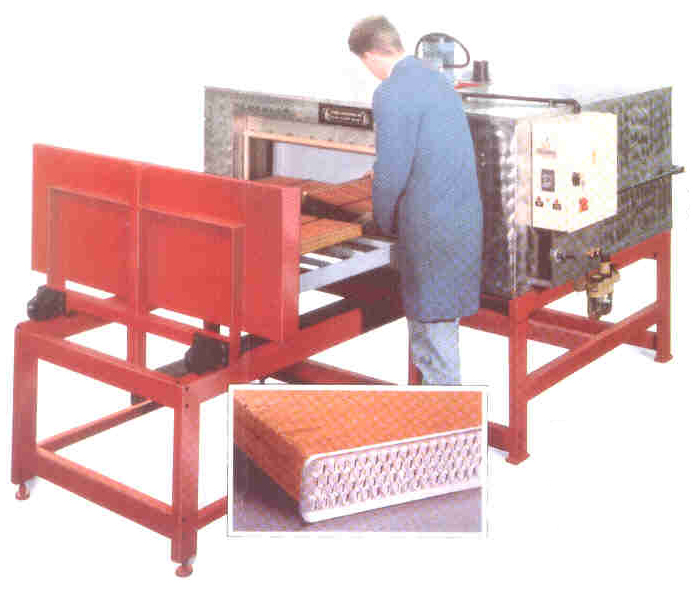 |
|
|
Plastic Tank machine | Tinning Machine |
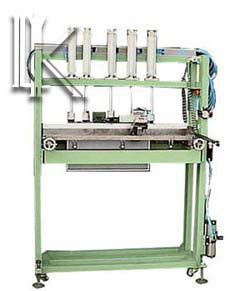 | 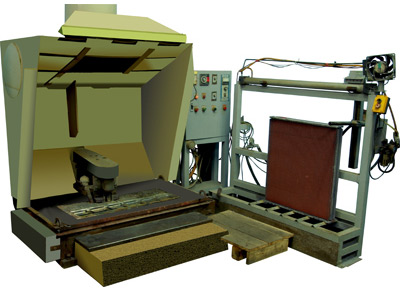 |